In the die design process, Yonetani’s approach is front loading to identify potential problems with the die manufacturing and molding operations. Our expertise is applied when conducting simulations for Flow, Heat Conductivity, Thermal Stress, Strength, and Particle flow analysis.
01
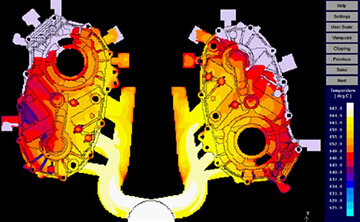
Casting defect countermeasures can be verified before the actual die modification.
The simulation results will differ depending on the parameters entered in CAD software. In order to match with the reality of the phenomenon, it is necessary to “analyze” the simulation results.
Yonetani has the ability to perform highly accurate and dependable verification with the database we have accumulated over the years of experience.
02
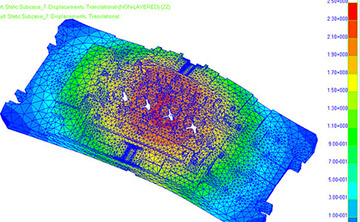
We can simulate how the design modification of the final casting product would affect its strength and die design.
The die could be deformed by stress due to the uneven distribution of heat and the clamping force. The magnitude of deformation can be predicted by the simulation in advance and we can design the die to minimize the deformation within the calculated tolerance.
03
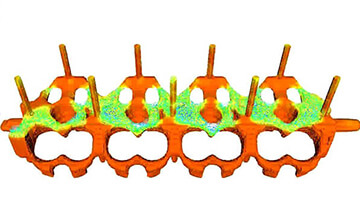
Yonetani can predict sand blockages and gas defects during the core molding.
In casting, we use a member called “core”, which is made of sand. This core is also molded with a mold. First, blow particulate sand into the mold, and harden the binder that has been kneaded with the sand that has been blown in advance by heat or chemical changes.
We can analyze and verify the state of filling and solidification of the sand in detail using the dedicated analysis software (Arena-Flow). As a result, the accuracy of
pre-verification such as blowing position and degassing can be improved, and it can contribute to the reduction of defective rate.